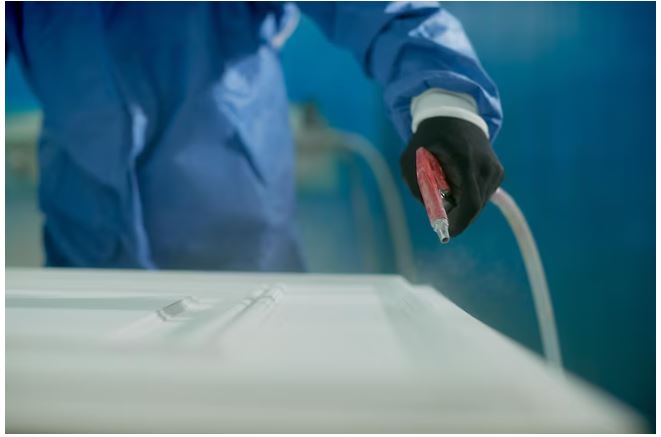
In industrial maintenance and restoration, the battle against rust has been a challenge. Traditional methods often involve abrasive techniques that not only consume time. They can also cause damage to the underlying surfaces. However, the emergence of laser rust removal technology has sparked a revolution in the field. It has offered a precise, efficient, and eco-friendly alternative.
Understanding Laser Rust Removal Technology
Laser rust removal operates on the principles of laser ablation. This is a process where a laser beam is used to remove rust and unwanted coatings from surfaces. The technology is built upon the absorption of laser energy by the material to be removed. When the laser beam interacts with the rust or unwanted substance, it causes rapid heating. This leads to vaporization and ejection of the material.
The Mechanics Behind Laser Ablation
The efficiency of laser rust removal lies in its precision. The laser selectively targets the unwanted material without affecting the substrate beneath. This precision is achieved through the careful calibration of laser parameters, including wavelength, pulse duration, and intensity.
Laser beams can be tuned to specific wavelengths that correspond to the absorption bands of the material to be removed. This targeted approach minimizes the risk of damaging the underlying surface, making laser rust removal suitable for a wide range of applications.
Applications Across Industries
The versatility of laser rust removal extends its applications across various industries. In manufacturing, where the quality of surfaces directly impacts product integrity, laser rust removal ensures a clean and pristine foundation for further processes. The automotive industry benefits from this technology. This is in the restoration of classic cars. It can also be used in the preparation of surfaces before painting.
Moreover, laser rust removal finds its place in historical preservation, where delicate artifacts and structures require careful restoration without compromising their structural integrity. The aerospace industry also embraces this technology for the maintenance of aircraft, ensuring optimal performance and longevity.
In the journey towards efficient and sustainable surface restoration, laser rust removal has emerged as a beacon of innovation. To delve deeper into the world of cutting-edge surface preparation technologies.
Advantages Over Traditional Methods
- Laser Precision
One of the most significant advantages of laser rust removal is its precision. Unlike abrasive methods, which can unintentionally remove layers of the substrate, laser technology allows for targeted removal of rust and contaminants, leaving the underlying material untouched.
- Minimal Environmental Impact
Traditional methods often involve the use of chemicals and abrasive materials that can be harmful to the environment. Laser rust removal eliminates the need for such materials, making it an eco-friendly alternative. The process produces minimal waste, contributing to sustainable industrial practices.
- Time and Cost Efficiency
Traditional methods can be time-consuming, requiring extensive labor and multiple steps. Laser rust removal, on the other hand, is a quicker process, reducing downtime and labor costs. The efficiency of laser technology translates into cost savings for industries seeking effective surface preparation solutions.
- Reduced Health Risks
Chemical methods and abrasive techniques pose health risks to workers involved in the process. Laser rust removal minimizes these risks by eliminating the need for harmful chemicals and reducing exposure to airborne particles generated during abrasive processes.
Challenges and Considerations
While laser rust removal presents a promising solution, it is essential to acknowledge potential challenges and considerations associated with the technology.
Material Compatibility
The effectiveness of laser rust removal depends on the material properties. Some materials may not absorb laser energy efficiently, limiting the applicability of this technology. Understanding the compatibility of materials is crucial for successful implementation.
Initial Investment
Acquiring laser rust removal equipment represents an initial investment for industries. While the long-term cost savings can outweigh this initial expense, businesses must carefully evaluate their specific needs and budget considerations before adopting the technology.
Operator Training
Operating laser rust removal equipment requires specialized training. Ensuring that operators are well-versed in the technology’s intricacies is essential for achieving optimal results and preventing potential safety hazards.
Future Implications and Innovations
As laser rust removal continues to gain traction, researchers and engineers are exploring innovative advancements to enhance its capabilities. Future iterations may involve the integration of artificial intelligence for real-time adjustments of laser parameters, further improving precision and efficiency. Additionally, developments in portable and handheld laser rust removal devices could expand the technology’s accessibility across various applications and industries.
Conclusion – A Paradigm Shift in Surface Preparation
In conclusion, laser rust removal stands as a transformative technology in the realm of surface preparation. Its precision, minimal environmental impact, time efficiency, and reduced health risks position it as a superior alternative to traditional methods. While challenges exist, ongoing research and advancements promise a future where laser rust removal becomes even more accessible and effective.